在智能制造升级过程中,3D 制造仿真已成为优化生产流程、降低试错成本的核心工具。但新手常因输入数据准备不足,导致仿真结果失真 —— 比如忽略机器故障数据导致瓶颈分析偏差,或遗漏物料流路径使产能测算失准。本文系统拆解 3D 制造仿真的6 大核心输入数据类型,结合Visual Components实战用例说明数据采集要点,助您从 “盲目建模” 转向 “精准仿真”。
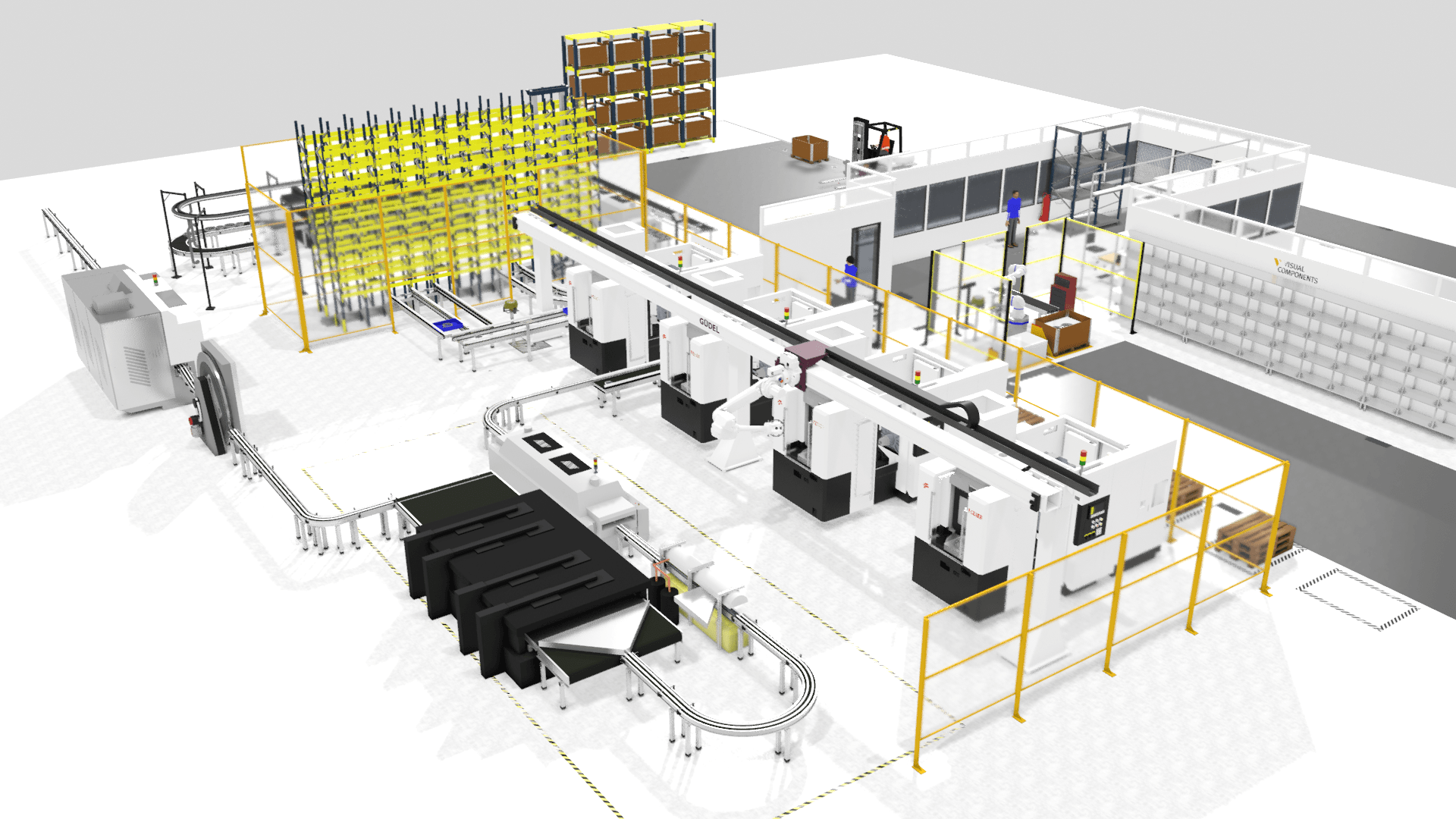
一、输入数据:决定仿真质量的 “地基”
3D 制造仿真的本质是通过数字孪生复刻生产场景,而输入数据的完整性直接决定复刻精度。如同盖楼需先明确地基承载力,仿真前需根据项目目标(如工厂优化、概念验证、虚拟调试)针对性采集数据。例如:
二、6 大核心输入数据类型及采集要点
1. 布局配置数据:仿真的 “空间骨架”
布局是仿真模型的物理基础,需包含两类关键信息:
采集技巧:用激光扫描生成工厂 3D 点云模型,或导出 CAD 布局图(支持格式:.step,.iges,.dwg),直接导入仿真平台(如 Visual Components)。
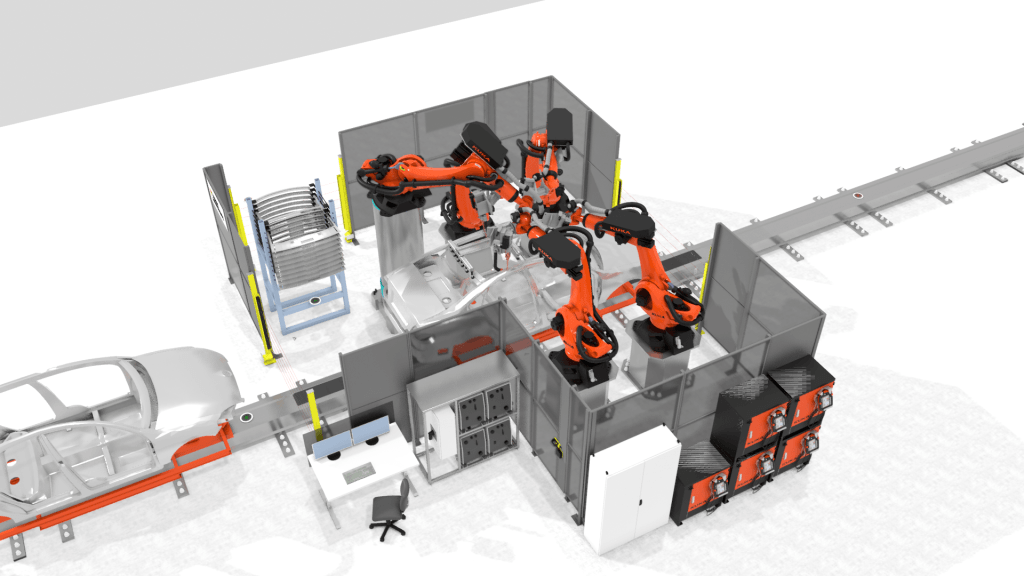
2. Visual Components 工厂物料流
了解物料在工厂中的流动对于精确仿真至关重要。这包括:
工艺路线:制造产品所需的一系列操作顺序,包括涉及的机器和工作站。这有助于理解工作流程并识别潜在的瓶颈。
生产订单计划:关于批量大小、装配顺序以及不同产品类型在工厂内流动的详细信息。这些数据对于规划和优化生产计划至关重要。
自定义组件属性:关于您的自定义组件(例如机器、AGV 或传送带)如何操作的信息,例如速度、设置时间和其他相关细节。了解这些属性有助于模拟生产阶段之间的时间和协调。Visual Components 还提供了 数千种行业标准组件(机器人、AGV、传送带),这些组件已包含来自设备制造商的此类数据。
3. 机器或特定工艺数据
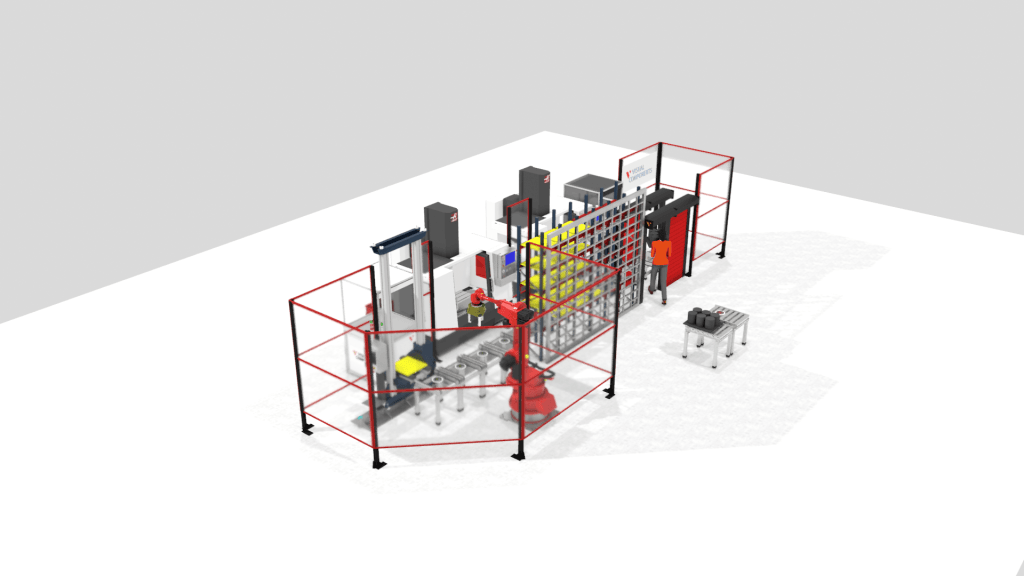
工厂内的每台机器或每个工艺都有可能影响仿真的特定数据:
机器故障发生情况:机器或工作站的修复前平均时间(MTTR)和平均故障间隔时间(MTBF)的历史数据。这些数据有助于模拟机器的可靠性和维护需求。
缓冲区容量:关于缓冲区库存位置及其容量的信息。这有助于管理库存并确保生产流程顺畅。
周期时间:单台机器或工艺的周期时间,可能因产品类型而异。这些数据对于精确的生产调度至关重要。
缺陷率:机器缺陷的历史数据。这有助于模拟质量控制流程并识别改进领域。
设置时间:更换产品类型时设置机器所需的时间。这对于规划生产变更和最小化停机时间至关重要。
4. 生产设施中的工作人员
人力资源是制造过程不可或缺的一部分。相关数据包括:
5. 产品数据
特定于产品的数据对仿真同样重要:
6. CAD 数据
Visual Components 擅长可视化仿真,而 CAD 数据对此至关重要:
三、3 大实战用例:数据应用场景详解
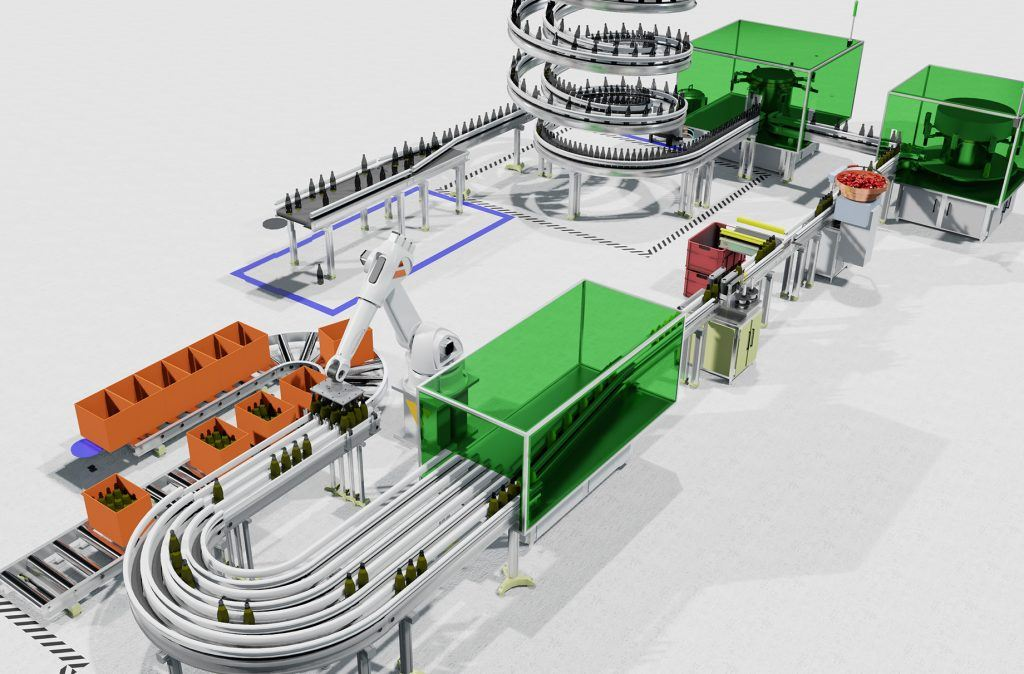
用例 1:大批量天线生产工厂优化
目标:提升 8 小时班次的天线产能,减少机器故障影响。
关键输入数据:
设备可靠性:各机器 MTBF/MTTR(如钻孔机 MTBF=120 小时,MTTR=1 小时);
物料流:闭环传送带托盘数量(测试 50/80/100 个托盘的产能差异)、工艺路线(“裁切→钻孔→组装→质检” 各步骤周期时间);
验证数据:历史 3 个月的实际产出量(用于校准仿真模型)。
成果:通过仿真发现 “托盘数量 80 个时产能最优”,结合故障预警机制,使班次产能提升 18%。
用例 2:机器人设备销售演示
目标:向客户展示机器人焊接工作站的效率。
关键输入数据:
布局 CAD:工作站 3D 模型(含机器人、工作台、安全围栏);
设备参数:机器人焊接速度(如 10mm/s)、工件装卸时间(20 秒 / 件);
简化数据:忽略复杂的故障数据,聚焦 “理想状态下的小时产能”;
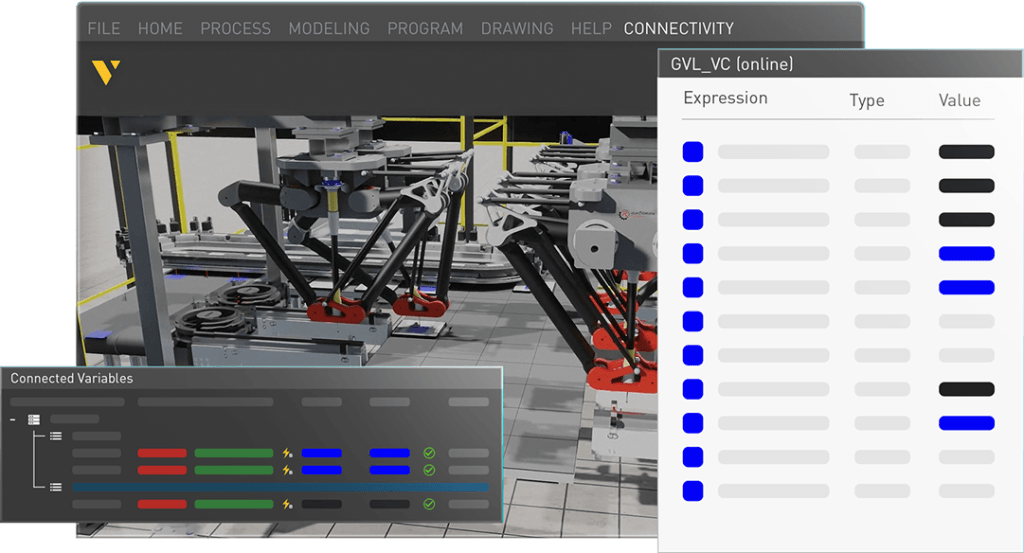
用例 3:Kawasaki 机器人虚拟调试
目标:在投产前验证机器人与生产线的信号交互。
关键输入数据:
信号映射:机器人 I/O 接口与传送带的信号对应关系(如 “信号 101 = 启动传送带”);
关节变量:机器人各轴运动范围(如 J1 轴旋转范围 - 180°~180°);
接口协议:机器人与 PLC 的通信协议(如 Profinet)。
价值:提前发现信号延迟问题,避免现场调试时的 2 小时停机。
四、数据采集工具与避坑指南
1. 工具推荐:
布局数据:用 Faro 激光扫描仪生成点云,导出为.ply 格式;
设备数据:从设备 PLC 导出运行日志(提取周期时间、故障代码);
物料流:用 MES 系统导出近 3 个月的生产订单与工艺路线。
2. 常见误区:
过度采集:为追求完美收集冗余数据(如记录与仿真无关的设备功率),拖慢建模效率;
数据过时:使用半年前的工艺路线,忽略近期生产流程调整;
格式错误:导入不兼容的 CAD 格式(如.skp 文件未转.step)导致模型缺失。
结论
本综合指南概述了在 Visual Components 中创建有效仿真模型所需的输入数据。通过理解并利用适合您特定用例的相应数据,您可以显著提升您的仿真结果。所需数据的类型和范围将根据您的行业和生产环境而有所不同,但这个灵活的框架将帮助您识别和收集成功仿真项目所需的相关信息。